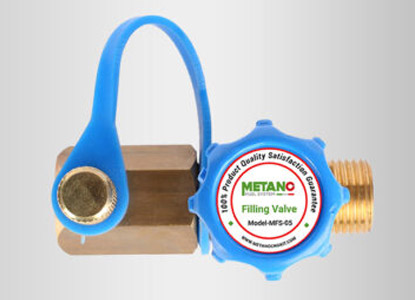
Filling valves are used in CNG (Compressed Natural Gas) vehicles to safely and efficiently transfer gas from the refueling station into the vehicle’s storage cylinder. Their primary application is in passenger cars, buses, trucks, and commercial fleet vehicles powered by CNG. The filling valve connects the dispenser nozzle at the fuel station to the vehicle fuel system, allowing high-pressure gas (usually around 200 bar) to enter the tank. It plays a critical role in ensuring a secure, leak-proof seal during refueling, preventing gas loss and maintaining safety. Some valves are equipped with non-return mechanisms to prevent backflow, enhancing safety further. Filling valves are also used in industrial CNG storage systems, where precise and safe gas handling is required.
Filling valves offer several important advantages in CNG systems, especially in vehicle applications. They provide a safe and secure connection between the fuel dispenser and the vehicle, ensuring that high-pressure gas is transferred without leaks. These valves are designed to handle extreme pressure, typically up to 200 bar or more, making them reliable for daily use. Many filling valves include a non-return (check) valve, which prevents gas from flowing backward, enhancing overall safety. They are also durable and corrosion-resistant, typically made from high-strength materials like stainless steel or brass. Filling valves ensure fast and efficient refueling, reducing downtime, which is especially important for commercial and fleet vehicles. Their compact design, easy operation, and compatibility with standard nozzles make them a convenient and essential component in all CNG-powered systems.
Filling Valves are a vital component of CNG fuel systems, ensuring safe, efficient, and leak-free refueling.